Tiny House in Progress
Although sustainability has
always been important to our practice, until now we hadn’t had the opportunity
to build a Passive House standard home.
Tiny House is currently in
the design phase and is expected to be completed in 2021. The name doesn’t
reflect its size; at 1200 square feet, it’s modest, but not extremely small. It’s
named, rather, for its location — in Tiny, Ontario
site in Tiny, Ontario
As the house is situated in
Georgian Bay, close to the beach and cross-country skiing trails, its owners
expect to host visitors year-round and to periodically work from home. Thus, extra
bedrooms double as offices, and the space can easily be divided in two for
privacy, or opened up for larger gatherings.
We’re using many
sustainable technologies on this project. The most important is a
high-performance building envelope. This means the walls, floor and roof will
be airtight, with a lot of insulation,
no thermal bridging (areas where building materials can transfer heat), and
careful consideration of the amount of glass and where it faces. Glass can be
used to avoid or benefit from solar heat gain at different times of year, but
in terms of airtightness, windows are always the weakest link, even with
triple-glazing.
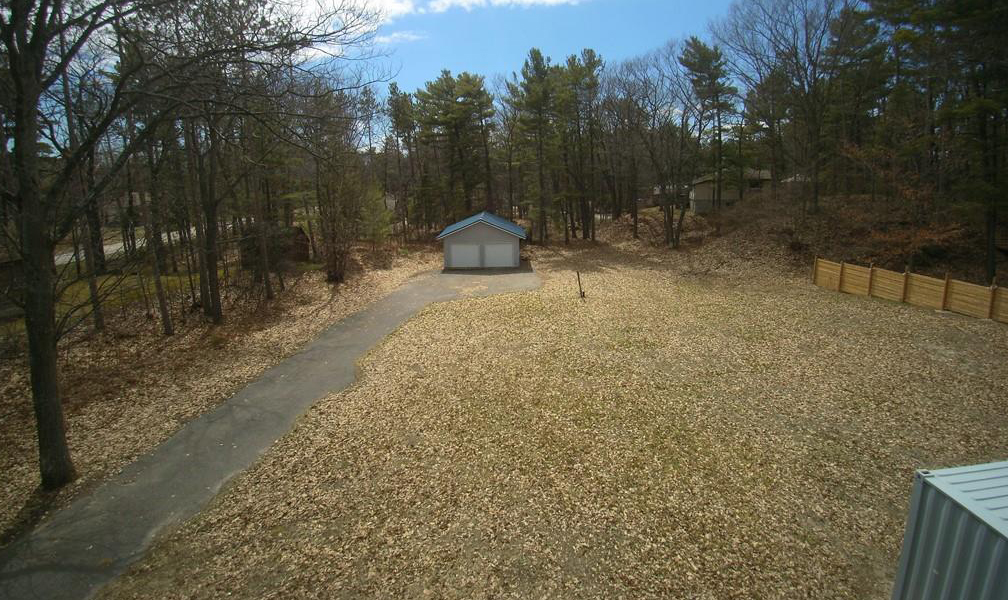
Tiny House site
A high-performance building
envelope improves thermal comfort and air quality, reduces unwanted exterior
noise, and allows the building to run on significantly less energy. The thick,
insulated and sealed walls do have a higher capital cost, but this is offset by
the savings on future heating and cooling bills, as well as the money saved on
the size of mechanical systems at the time of building.
Since the airtightness of the
building’s exterior is so important, constructing to the Passive House standard
requires an exactness that is difficult to achieve in the field.
Contractors who understand the Passive House principles and how to craft the details can be hard to find. For that reason, we are exploring the possibility of constructing the walls and roof — complete with structure, insulation and windows — offsite. That way, once the contractor on location has prepared the site and insulated slab, they’ll only need to assemble the wall and roof panels, which will have been prefabricated in a controlled factory environment.
To meet the R-value, or level of thermal resistance, required by the Passive House standard, the walls need to be very thick. This lends itself well to deep sills for cozy window seats.
Also, the wood frame on the interior can be left exposed for visual interest and to provide small shelves, inspired by William Turnbull, Jr.’s Hine House at Sea Ranch.
Contractors who understand the Passive House principles and how to craft the details can be hard to find. For that reason, we are exploring the possibility of constructing the walls and roof — complete with structure, insulation and windows — offsite. That way, once the contractor on location has prepared the site and insulated slab, they’ll only need to assemble the wall and roof panels, which will have been prefabricated in a controlled factory environment.
To meet the R-value, or level of thermal resistance, required by the Passive House standard, the walls need to be very thick. This lends itself well to deep sills for cozy window seats.
Also, the wood frame on the interior can be left exposed for visual interest and to provide small shelves, inspired by William Turnbull, Jr.’s Hine House at Sea Ranch.
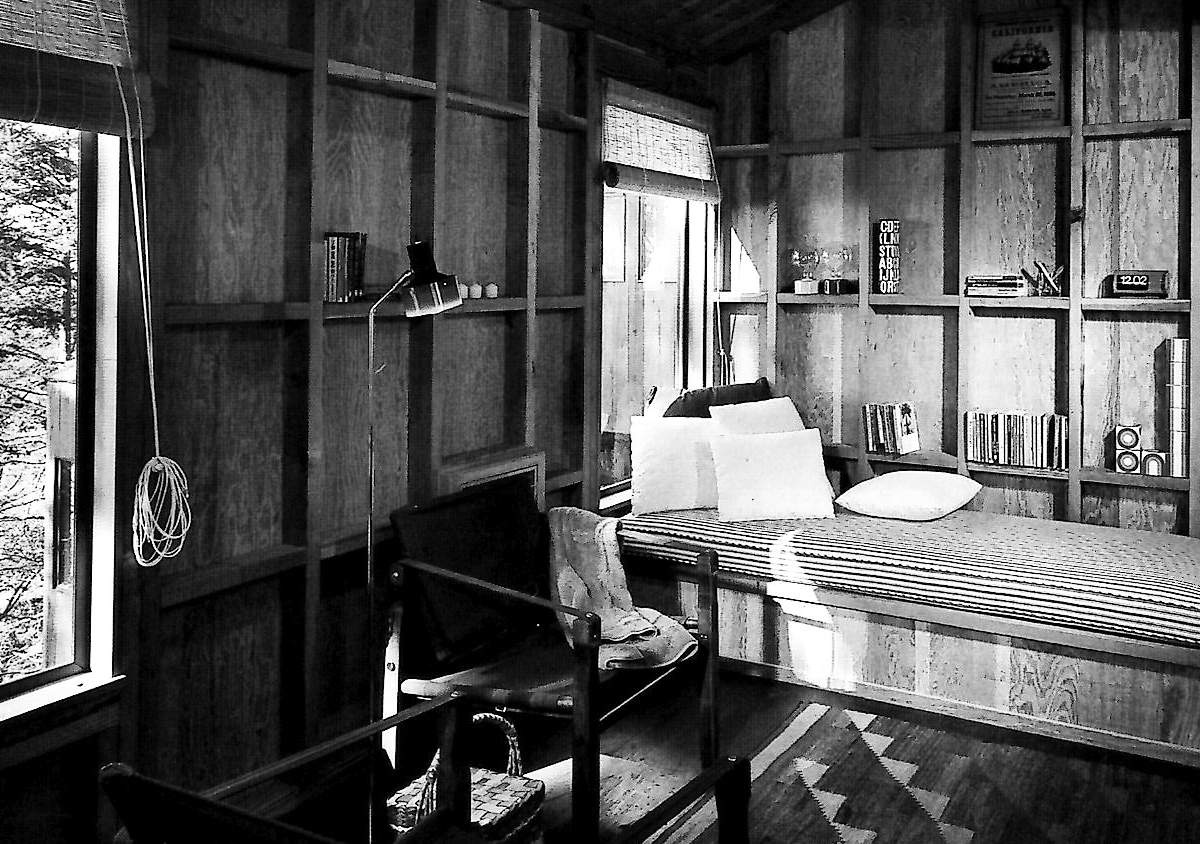
Hines House at Sea Ranch designed by architect William
Turnbull, Jr. in 1968.
“In the sixties, we did a series of what I call wall houses. We took the wall, opened it up, and hung saddlebags on it.” William Turnbull, Jr.
Text by David Colussi,
Director at WORKSHOP, a Certified Passive House Designer and designated a
Building Science Specialist in Ontario.