Unfinished House

The name “Unfinished House” refers to an aesthetic attitude, an approach to material reduction, and budget restraint that leaves parts of the design incomplete.
The house looks raw and unvarnished.

There is no soffit to hide the underside of the roof deck and wood framing at the overhangs.

The two bedroom, two bathroom home is a pilot for panelized prefabricated construction. It has a high-performance envelope and low-carbon foundation.


PHOTO SUPPLIED BY EVOLVE BUILDERS
The home has no basement to keep the concrete/carbon footprint to a minimum, so the heat pump and ERV units are tucked into the roof line, accessed from a catwalk on the mezzanine.


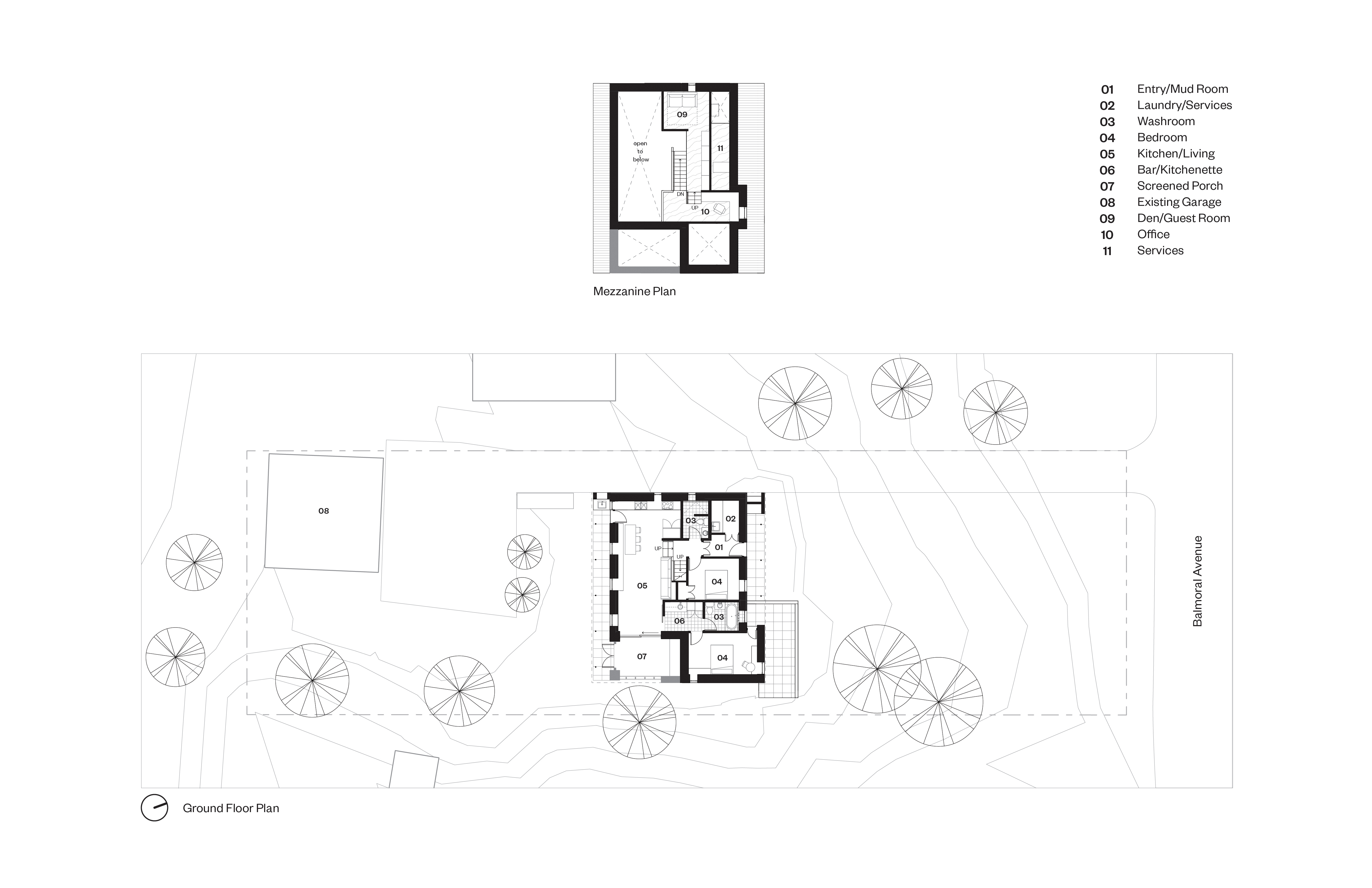
FLOOR PLANS
As the insulation is outboard (on the exterior side of the vapour barrier), the douglas fir plywood sheathing and pine framing is left exposed on the interior for visual interest.
![]()
WALL SECTIONS
The depth of the wall framing is used for small storage shelves in the kitchen – a detail inspired by William Turnbull, Jr.’s Hine House at Sea Ranch.
![]()
HINE HOUSE INTERIOR, SEA RANCH, 1968

WALL SECTIONS
The depth of the wall framing is used for small storage shelves in the kitchen – a detail inspired by William Turnbull, Jr.’s Hine House at Sea Ranch.
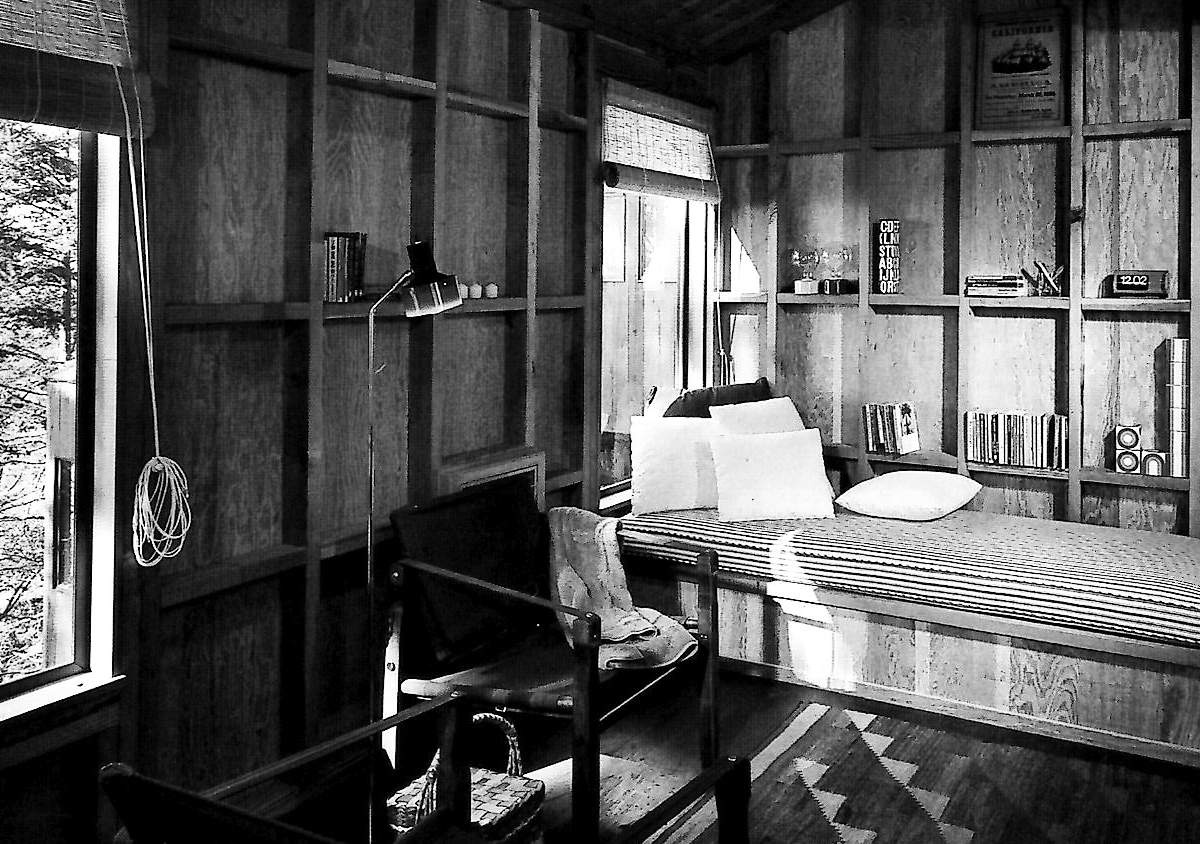
HINE HOUSE INTERIOR, SEA RANCH, 1968

The design language, materiality and colour selection of the home is taken from rural Ontario forms and beach house vernacular as the area mixes farms, seasonal homes and year-round residences.
![]()
Small details make for comfortable living and energy reduction – for example, eyebolts welded onto exterior steel columns support a clothesline for hanging beach towels, laundry and shades to the south.
Unlike many contemporary projects, there is a purposeful restraint in glazing. This is a suburban-scaled site, but with the careful window placement there is a feeling of being alone in the pine oak savanna landscape.
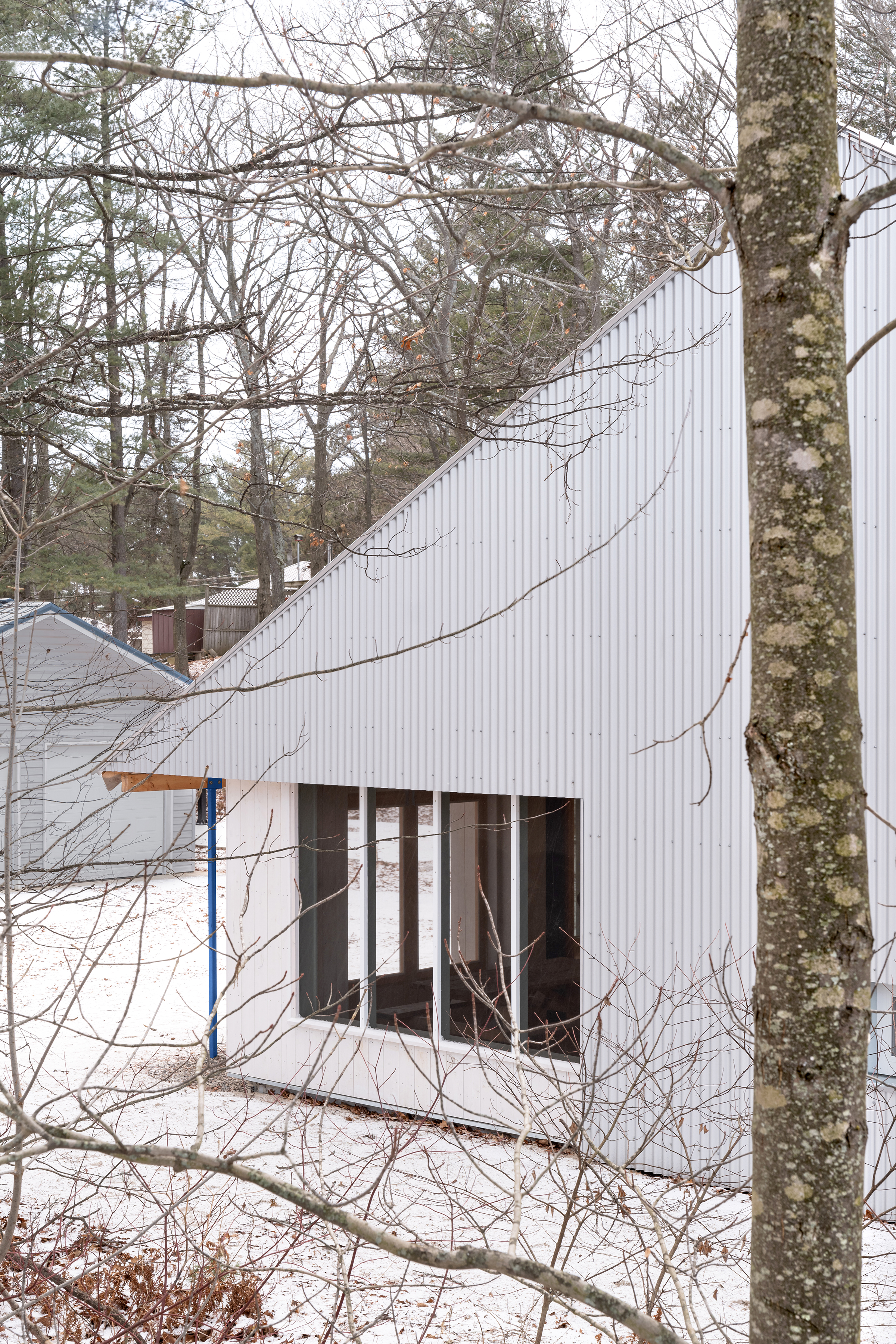

Small details make for comfortable living and energy reduction – for example, eyebolts welded onto exterior steel columns support a clothesline for hanging beach towels, laundry and shades to the south.



Unlike many contemporary projects, there is a purposeful restraint in glazing. This is a suburban-scaled site, but with the careful window placement there is a feeling of being alone in the pine oak savanna landscape.

Windows
are placed to maximize cross-ventilation from the lake breezes.
For privacy, the only windows on the two
sides are small square vents.


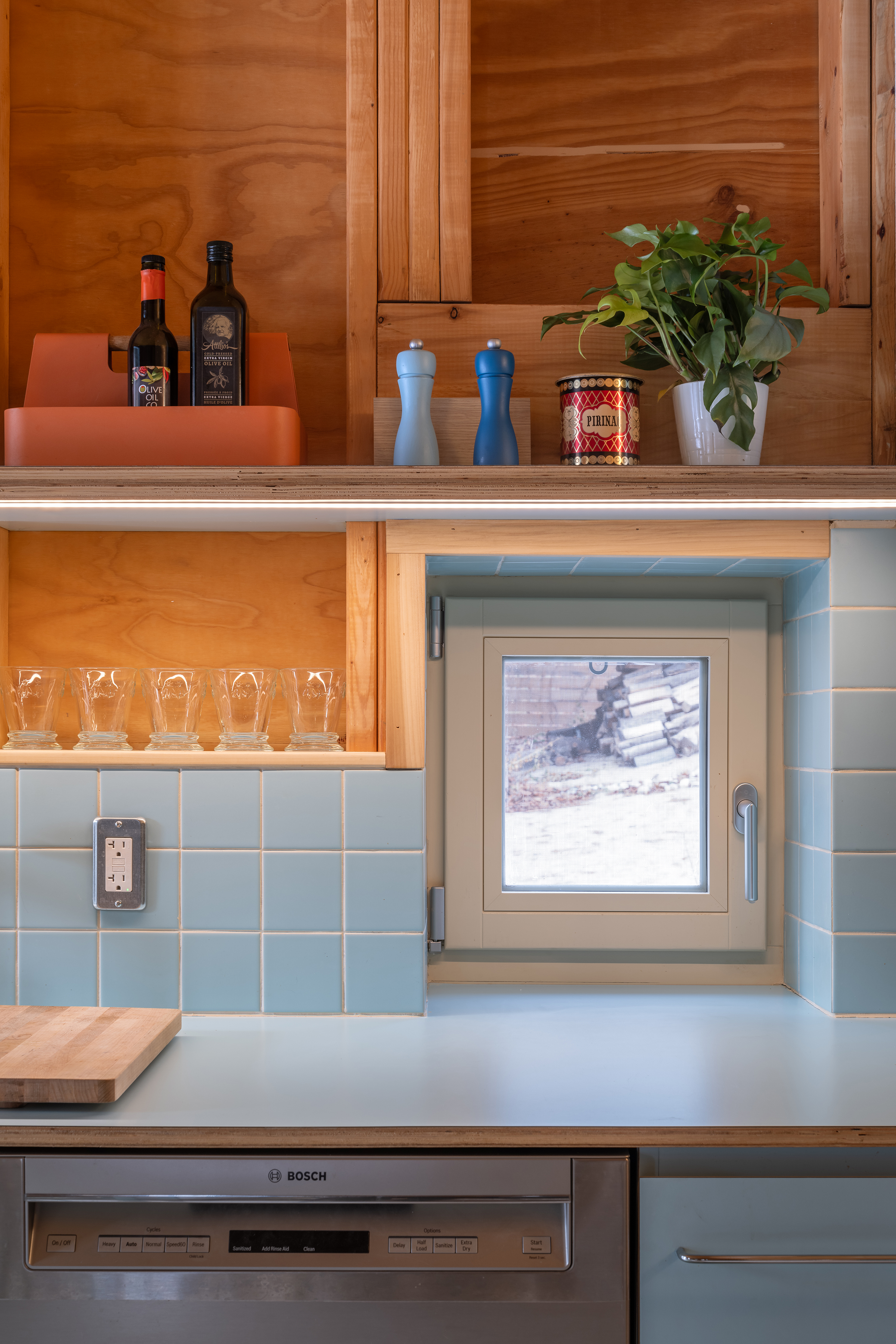
The thick, highly-insulated walls create deep window sills that are placed at seating, desk and counter heights to make use of the extra space.
Self-finishing materials were selected to reduce resources and reveal the building’s component parts.
![]()
![]()
Tile and spruce plywood are the only extra finishes, located in areas with wiring and plumbing.


Tile and spruce plywood are the only extra finishes, located in areas with wiring and plumbing.


The millwork is plastic laminate with exposed birch plywood edges and integral pulls.

The flooring is the exposed frost-protected shallow concrete slab foundation.
PHOTO BY WORKSHOP.
The home has a self-contained in-law suite with its own exterior door. An internal sliding door connects the two units, the kitchenette then doubles as a bar for the screened porch.
![]()




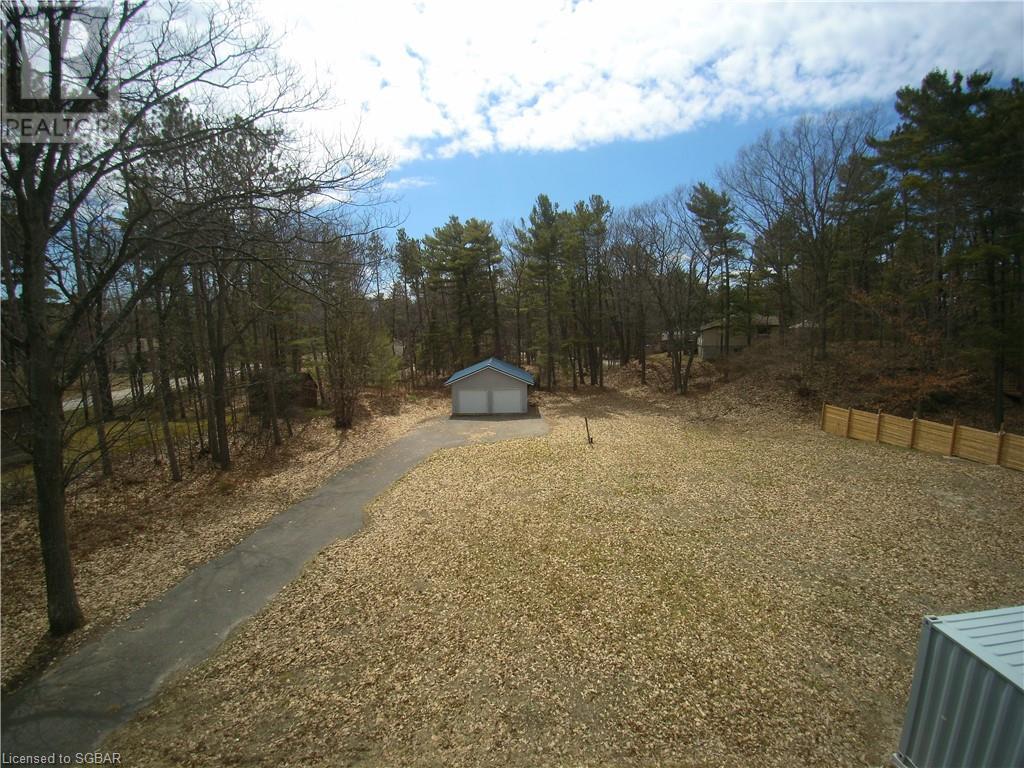
SITE BEFORE CONSTRUCTION.
PHOTO COURTESY OF MLS LISTING.
PHOTO COURTESY OF MLS LISTING.
Offsite construction was selected to reduce waste, to speed up installation time and to improve quality/performance.
During the design stage the architects shared a computer model back and
forth with the fabricator.
All the framing elements
were modelled, which allowed air barrier continuity to be considered at panel
joints in 3D.
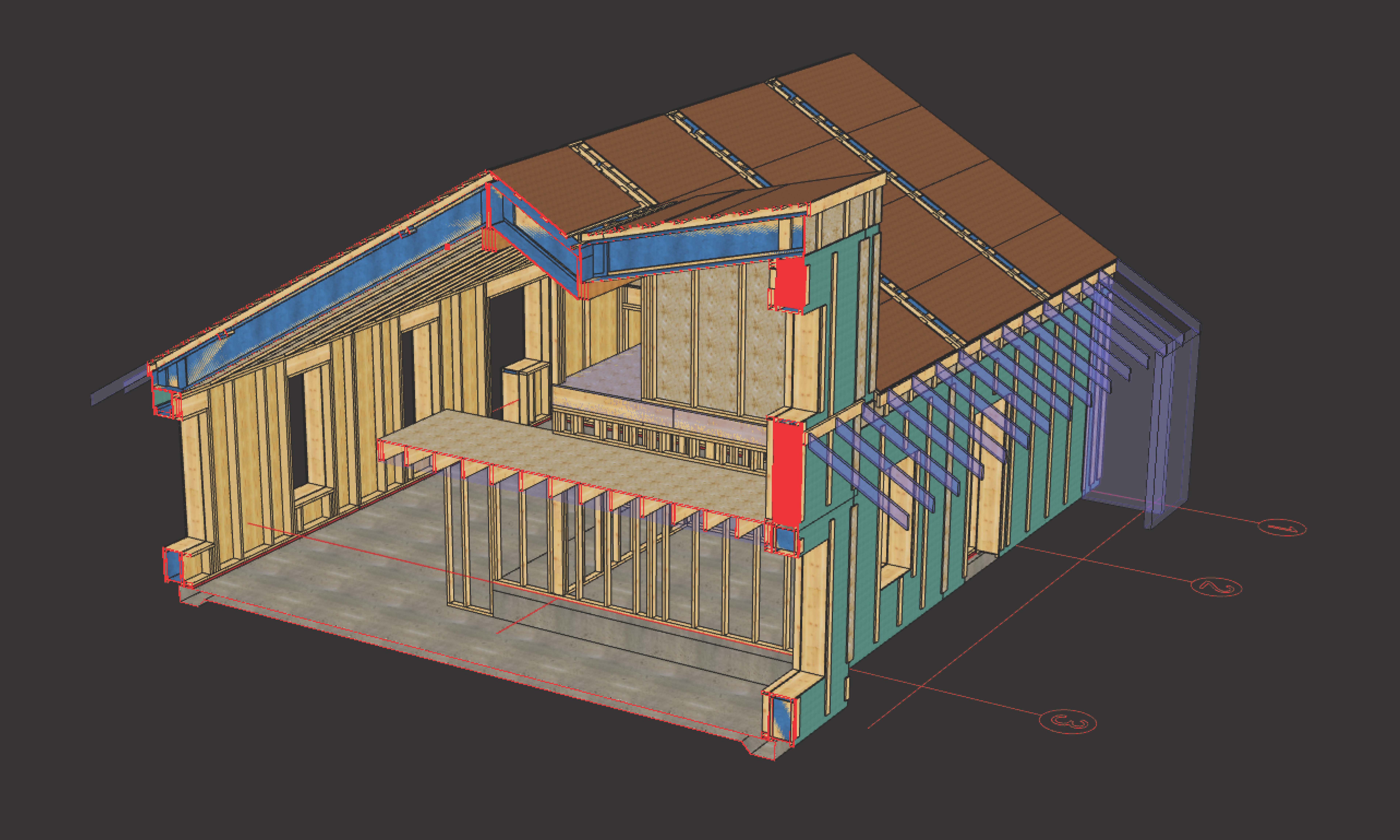
Plumbing and electrical services were grouped into areas to be concealed, complete with in-slab conduit stubs to avoid passing through areas of visual-grade exposed framing.

The house is specific to the
site, not a kit of parts meant to be repeated.
The design and construction process – using a panelized high-performance envelope – is repeatable. Panelized prefabrication is much more flexible spatially and easier to transport than volumetric modular prefab, so it is more readily applied to a range of building projects.
After testing a high performance prefab panel in this small project, we are now using them to overclad an existing 16-unit seniors residence for the Toronto Community Housing Corporation to meet EnerPHit (the Passive House standard for renovations).
By using a panel system, residents will be able to stay in place during construction. On-site construction time, dust and noise can be minimized, and the building’s energy and green-house gas use will be reduced by 90%.
The design and construction process – using a panelized high-performance envelope – is repeatable. Panelized prefabrication is much more flexible spatially and easier to transport than volumetric modular prefab, so it is more readily applied to a range of building projects.

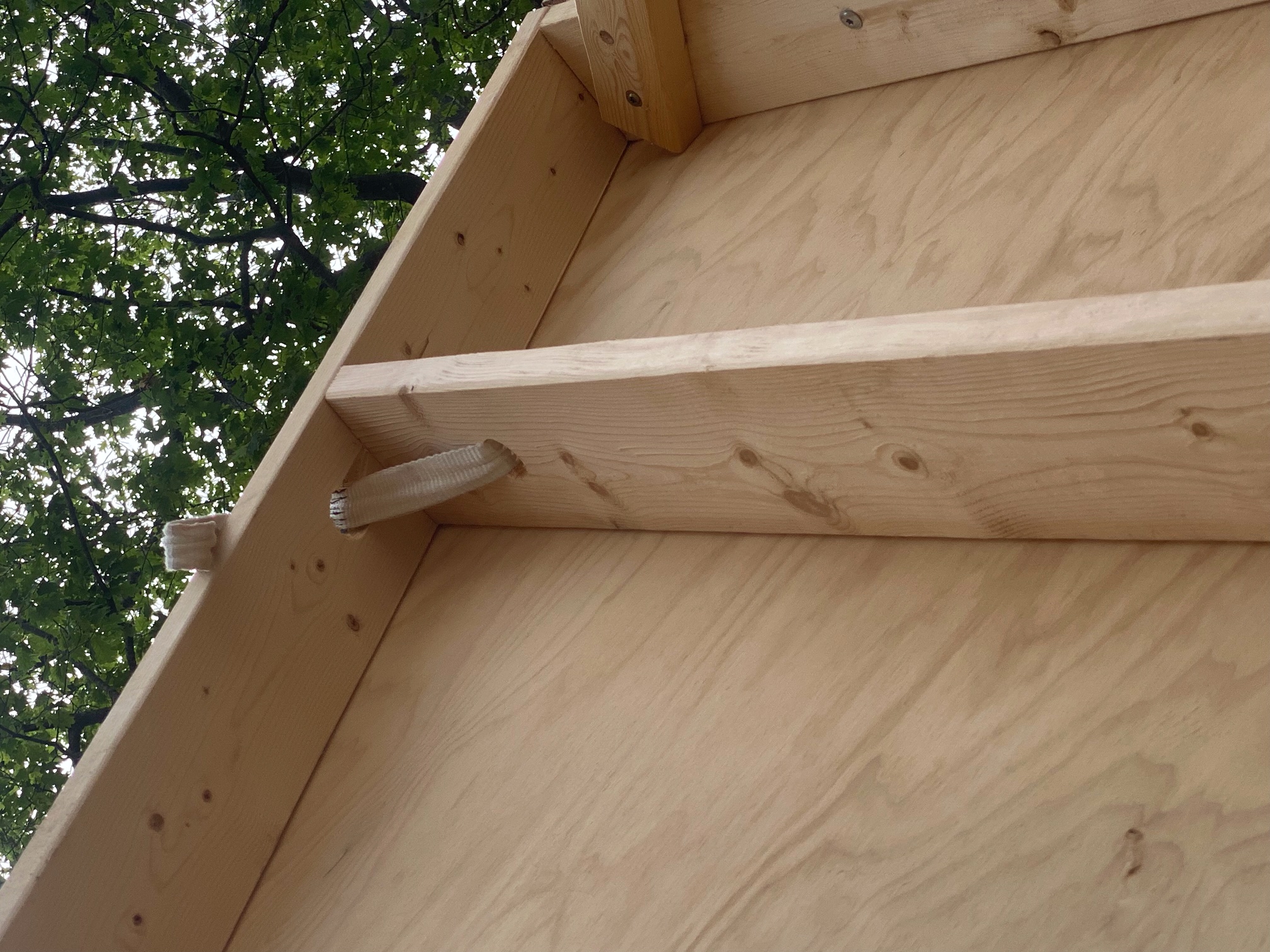





PHOTOS BY EVOLVE BUILDERS, WORKSHOP + VISUAL ROOTS PHOTOGRAPHY (4th + 5th PHOTOS FROM THE TOP)
After testing a high performance prefab panel in this small project, we are now using them to overclad an existing 16-unit seniors residence for the Toronto Community Housing Corporation to meet EnerPHit (the Passive House standard for renovations).
By using a panel system, residents will be able to stay in place during construction. On-site construction time, dust and noise can be minimized, and the building’s energy and green-house gas use will be reduced by 90%.
— David Colussi“ For us the project was a test to first understand the constraints of off-site fabrication, and then to push these limits. For example, by using visual grade wood for the framing and sheathing (a first for the panel manufacturer) we sought to expand the already impressive waste reduction and material economy potential presented by the prefabrication process.”
Proud to be a 2024 Best of Canada winner!
Check out the article in Dwell and in Dezeen where it was the most popular house in April 2024!
Client: WORKSHOP
Location: Tiny, Ontario
Date: 2022
Architecture team: David Colussi, Helena Grdadolnik, and Nina Hitzler
Engineering: Konsolidated Structural and CK Engineering
Simple Life Homes built the Passive House standard high performance prefab wall and roof panels in Cobourg, Ontario. Evolve Builders and Muskoka River Fine Homes provided the climate conscious construction.
photos by Scott Norsworthy (EXCEPT WHERE NOTED)
Location: Tiny, Ontario
Date: 2022
Architecture team: David Colussi, Helena Grdadolnik, and Nina Hitzler
Engineering: Konsolidated Structural and CK Engineering
Simple Life Homes built the Passive House standard high performance prefab wall and roof panels in Cobourg, Ontario. Evolve Builders and Muskoka River Fine Homes provided the climate conscious construction.
photos by Scott Norsworthy (EXCEPT WHERE NOTED)